The CleanFill Hub
Find out what happens at our CleanFill Hub to make our circular system tick. From laser etching QR codes to direct-to-container label printing, we've solved some challenging problems in innovative ways to make it work.
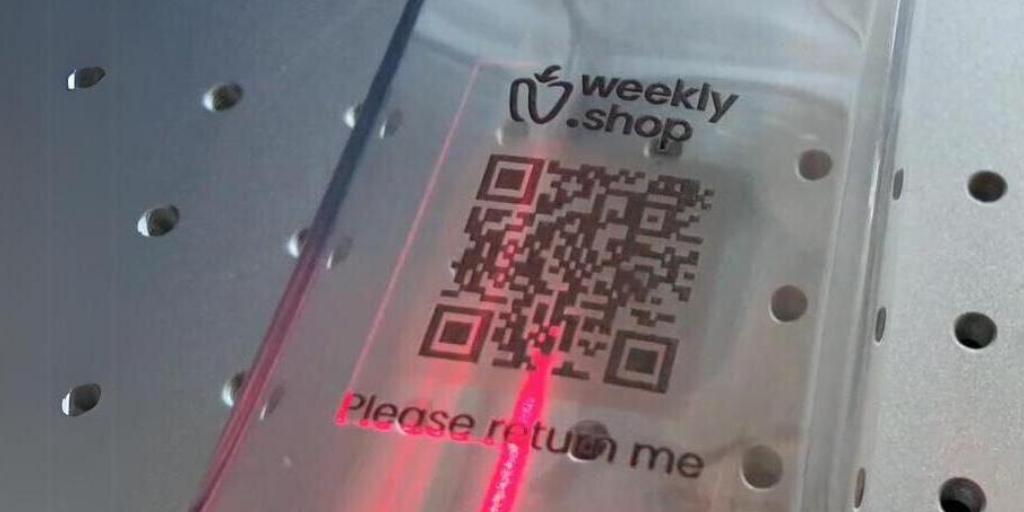
We hope this gives you a good overview. We're going to be going into much more detail on how we do it, what containers are made of, safety and so much more in the future so do stay tuned.
The CleanFill Hub is designed to operate all the steps in our circular system itself. We don't outsource any of the core process, allowing us to keep better control of quality and cost - ultimately making our products cheaper for our customers.
The flow goes like this:
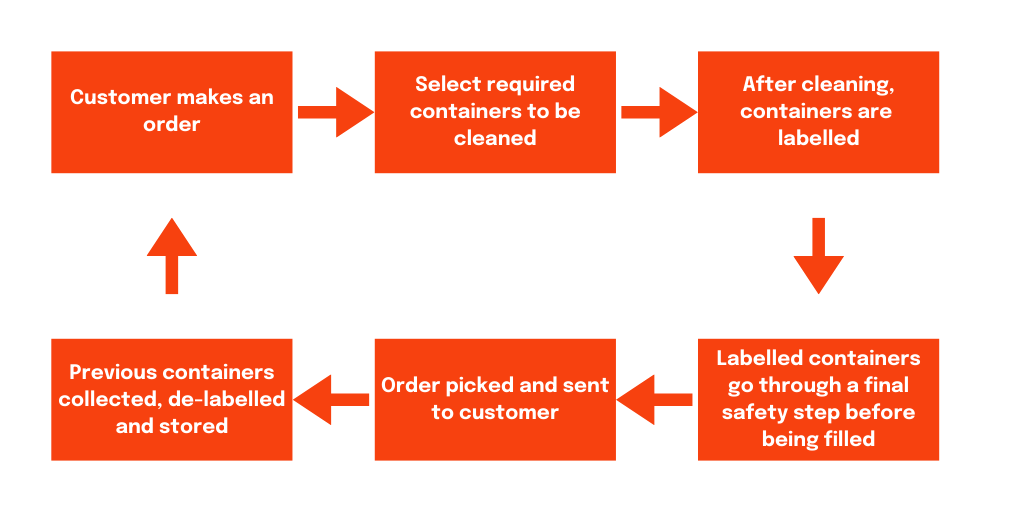
Here's a little more detail on each of the things the CleanFill Hub does.
- Delivery and collection
We use electric assisted cargo bikes to make our rounds. Here's Mark testing one out earlier this year:
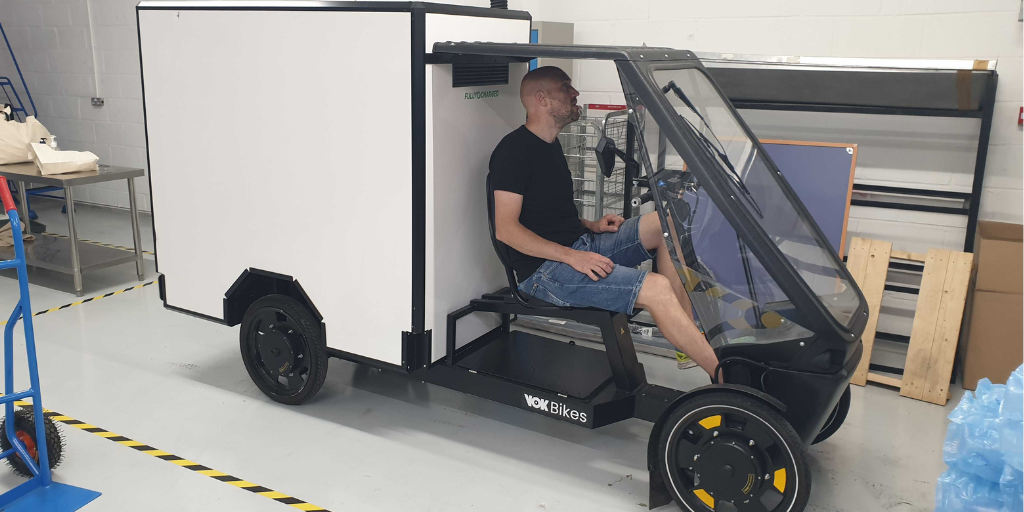
- De-labelling and labelling
In the circular economy, it's important to be able to use the same containers for different products. This means you need to remove a label, which are typically made of paper or plastic and glued on with adhesive. Removal is messy and creates packaging waste, as well as taking time and costing money.
To address this, and to stay true to our zero waste maxim, we decided not to use conventional labels.
However, there is legislation that guides product labelling that governs the information you need to provide to customers, claims you can make, as well as safety and warning information for allergens or hazardous substances.
So, we simply apply this information directly to the bottle, with an in house print innovation that we call MagicLabels.
No paper, plastic or glue, and we're able to remove them easily before the cleaning process, the only residue is a minute amount of carbon black.
The system is powered by our own software, including a custom built label editor that let's us easily manage and edit thousands of labels.
Nobody has done this before.
This is how they look, you can also see examples throughout the personal and home care sections of our website:
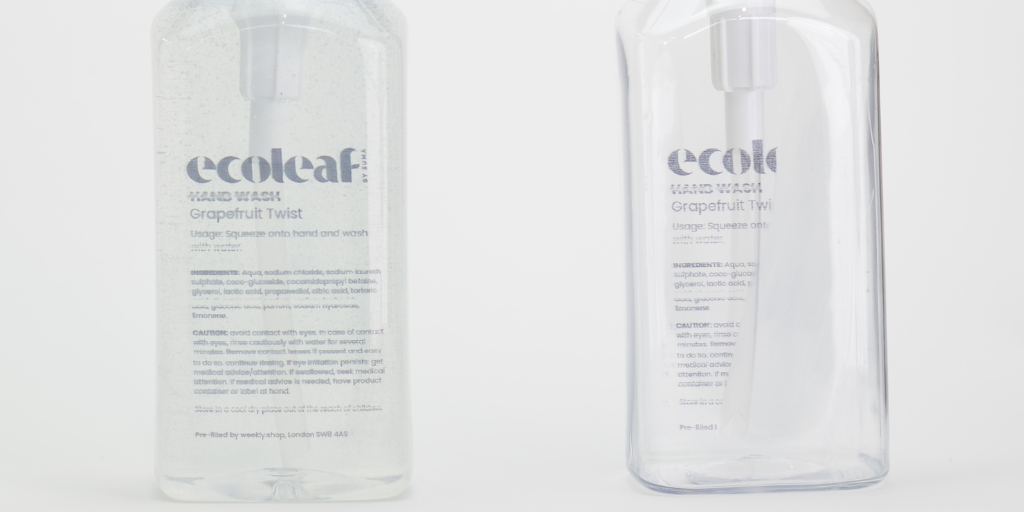
- Container cleaning
We clean containers ourselves so that we can do it on demand. This happens right before they are used, which means:
- They are as clean as when they were new when we fill them
- We need less containers
- We don't have to wash things again if they've been sitting in storage "clean" for a long time
Note that if something comes back very dirty it'll get cleaned before being stored as dirty, it will still get cleaned again when it gets used.
To ensure safety in both cleaning and filling (see 4. below) we operate a HACCP designed and audited by our Food Technician who is Food Safety Level 4, has a BsC Food & Consumer Management, and is a SALSA Mentor & Auditor. We use hygiene swabs, calibration checks and temperature logging to validate efficacy.
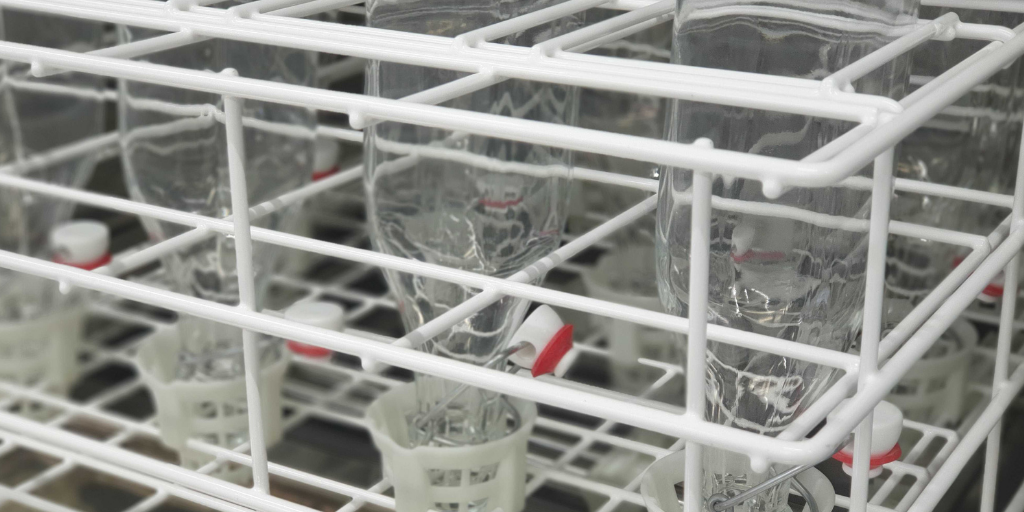
- Filling.
We fill everything on site. From milk to pasta, hand wash to bathroom cleaner.
This micro fulfilment approach is very efficient, and the just-in-time production of products keeps both prices and the number of containers we need lower.
We call this stage fulfilment, and it's powered by another first...
- ZeroTrace
We laser etch a scannable ID (QR code) onto every container. Each ID is unique, allowing us to track each container through every step of it's life.
This is fantastic for understanding the environmental and commercial life cycles of containers, and it also gives us excellent traceability.
In the (near, we think) future we'll be able to add features such as "scan to reorder" for customers too, as QR codes now widely read by smart phones.
We use lasers because it means no waste (no permanent sticker), and easy end of life recyclability (no difficult extraction of an embedded RFID chip required).
Nobody has done this with lasers before.
Here is the laser in action on a plastic hand wash bottle:
As you've found out, a lot has gone into making the system work.
With an end result that's easy to use zero waste shopping, we believe it's been worth it.
If you have any further questions about how it works, please do get in touch with us by email, phone or send us a message via live chat.